Industry 4.0 is a revolution that involves not only cutting-edge technology, but also production models and management concepts aimed at achieving higher efficiency, intelligence, automation, and informationalization. These elements require synergy to achieve end-to-end digital integration covering the whole life-cycle management. In the realm of electronics manufacturing, PCBA manufacturing faces challenges related to high precision and process traceability.
In SMT process, reflow soldering holds the significant importance to solder PCB and components firmly with solder paste. To ensure the soldering quality and reliability, the temperature testing in inflow soldering is essential. A reasonable temperature curve setting can avoid soldering defects like cold solder joint, bridging, and etc.
The precision and traceability ensure that the entire manufacturing solder process complies with high standard certifications which are exactly required by industries such as vehicles, medical apparatus and instruments, which are trendy now and in the future. Online furnace temperature monitoring systems are indispensable tools in the PCBA manufacturing landscape. Zhuhai Xinrunda Electronics has been well-equipped and manufacturing high quality and reliable PCBA for high production yield, sophisticated and complex electronic devices. Contact us for inquiry and let us help you transform your designs into flawless assemblies - where precision meets reliability, and innovation powers your next breakthrough!
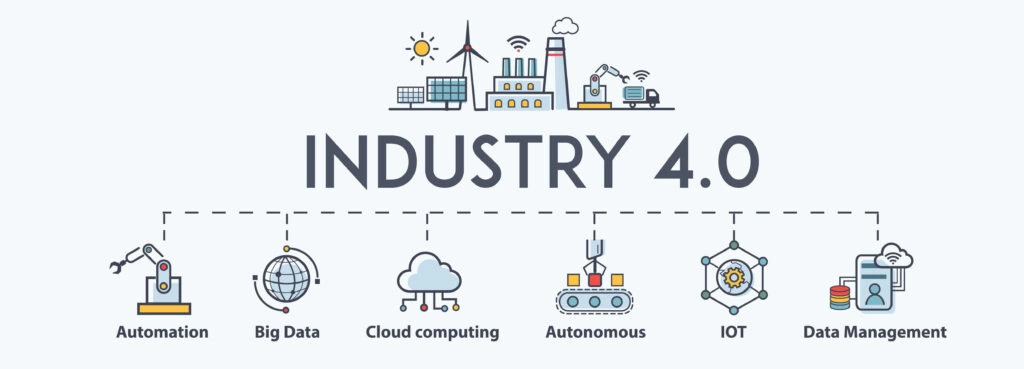
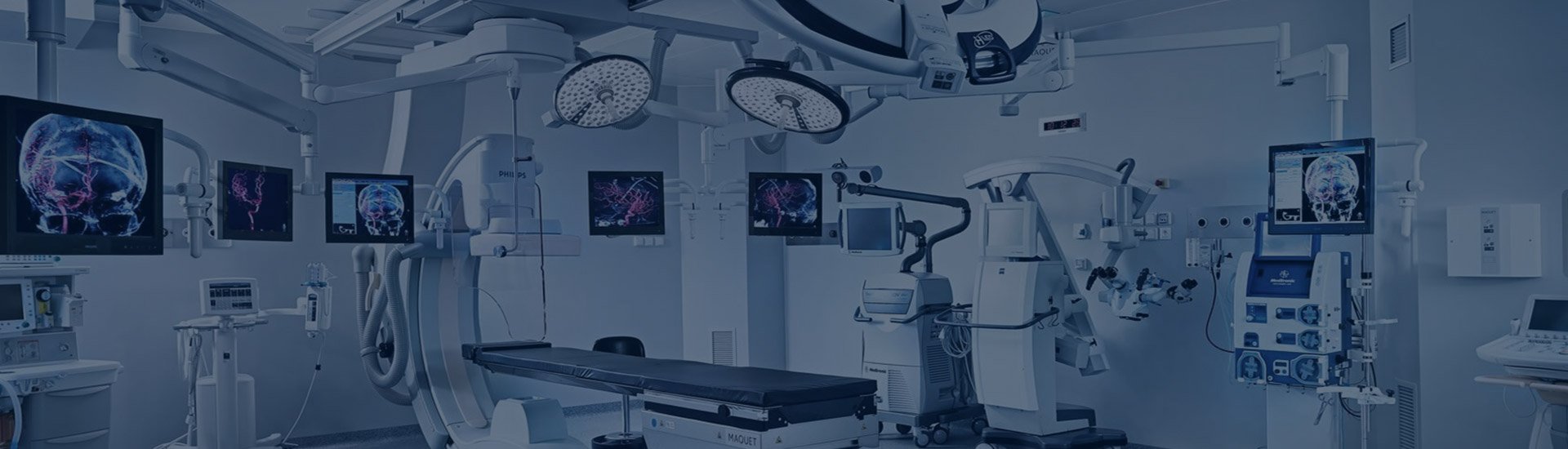
In most practices, a furnace temperature tester and a temperature measuring plate are connected correctly and manually, and sent into the furnace to obtain the temperatures in soldering, reflow soldering or other thermal processes. The temperature tester records the whole reflow temperature curve in the furnace. After taken out of the furnace, its data can be read by a computer to confirm whether it meets the requirements. Operators will correct the temperature cures and run the above testing process repeatedly till the optima. It’s obvious that the achieving precision costs time. Even thought it is the effective and reliable way of confirming the temperature, the testing is unable to detect production abnormalities because it is typically only conducted before and after production. Poor soldering doesn’t knock, it appears silently!
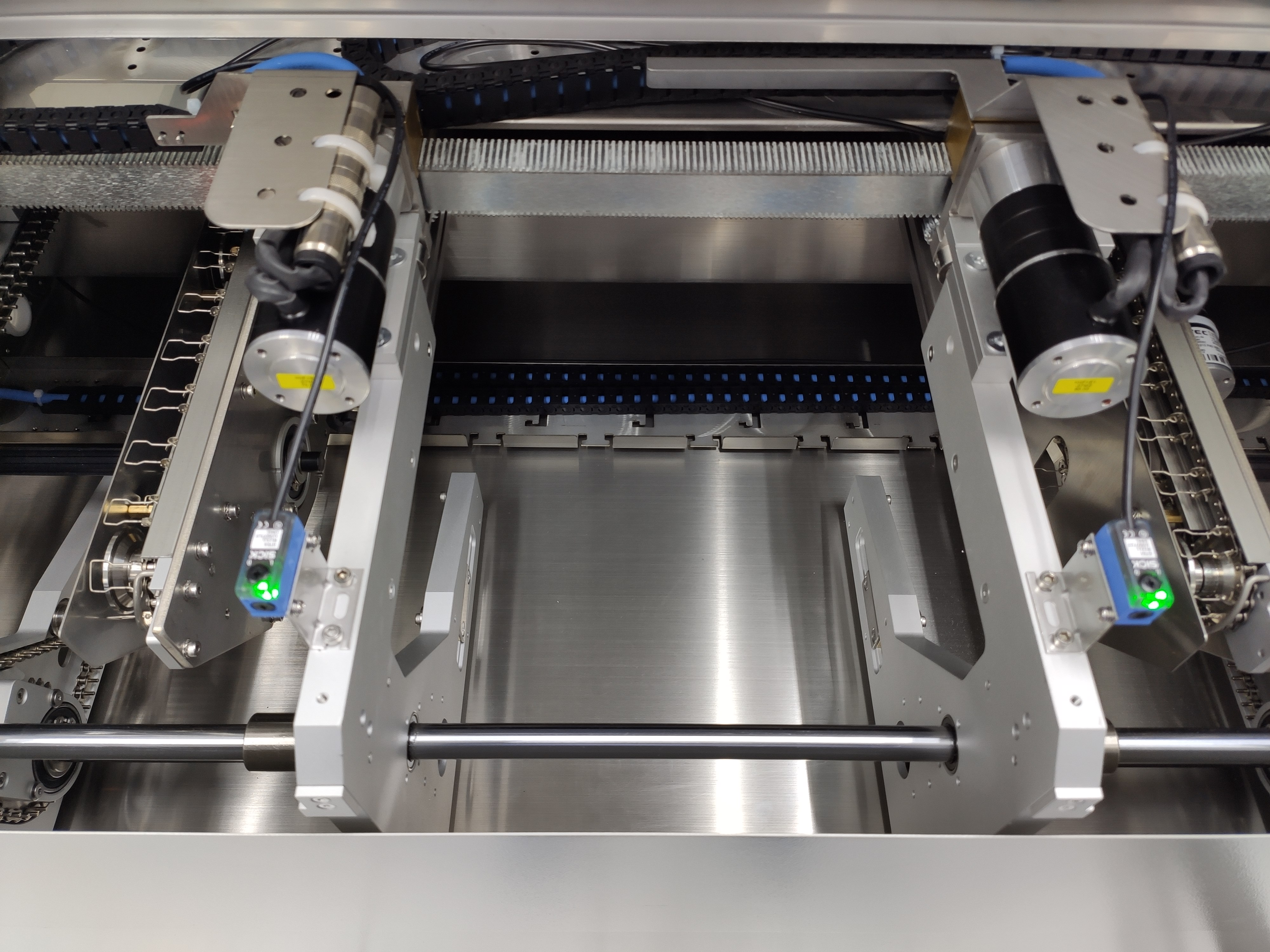
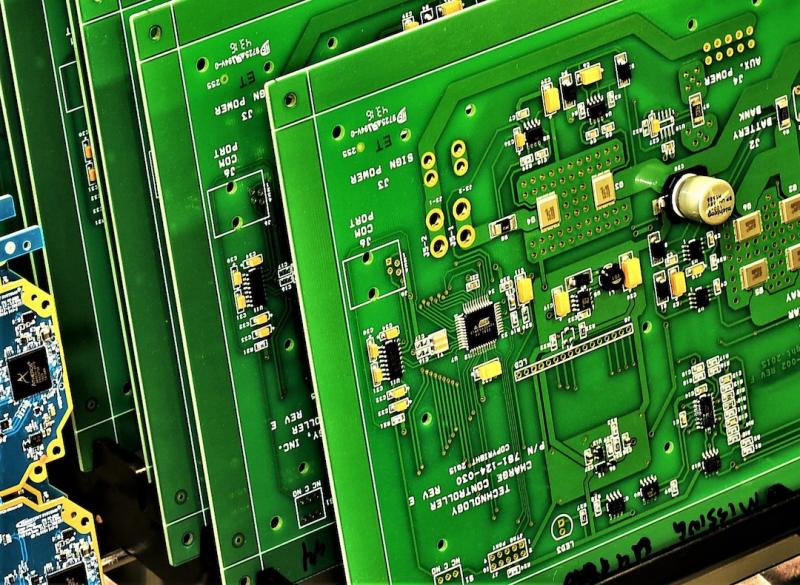
To elevate the PCBA production process to new heights of quality, efficiency, and safety, an online furnace temperature monitoring system is a pivotal technology.
By continuously monitoring the temperatures inside the furnace used for soldering, the system can automatically obtain temperatures of each PCB in processed and match. When it detects a deviation from the set parameters, an alert will be triggered, allowing operators to take corrective action promptly. The system ensures that the PCBs are exposed to the optimal temperature profiles to minimize the risks of soldering defects, thermal stress, warping, and component damage. And the proactive approach helps prevent costly downtime and reduce the incidence of defective products.
Let’s take a closer look at the system. We can see that two temperature sticks, each equipped with 32 uniformly distributed probes, are installed in the furnace to sense internal temperature changes. A standard temperature curve is preset in the system to match with the real-time changes of PCB and furnace, which are automatically recorded. Along with temperature probes, other sensors are equipped for chain speed, vibration, fan rotation speed, board entry and exit, oxygen concentration, board drops, to generate data such as CPK, SPC, PCB quantities, pass rate and defect rate. For some brands, the monitored error value can be less than 0.05℃, time error less than 3 seconds, and slope error less than 0.05℃/s. The system’s advantages include high-precision monitoring curves, fewer errors, and facilitation of predictive maintenance by identifying potential issues before they escalate to severe problems
By maintaining the optimal parameters in the furnace and reduces the likelihood of defective products, the system boosts the production yields and enhances efficiency. In some cases, the defective rate can be reduced by 10%-15%, and the capability per unit time can be increased by 8% - 12%. On the other hand, it minimizes energy wastage by precisely controlling the temperatures to remain in the desired range. This not only reduces operational costs but also aligns with the growing emphasis on sustainable manufacturing practices.
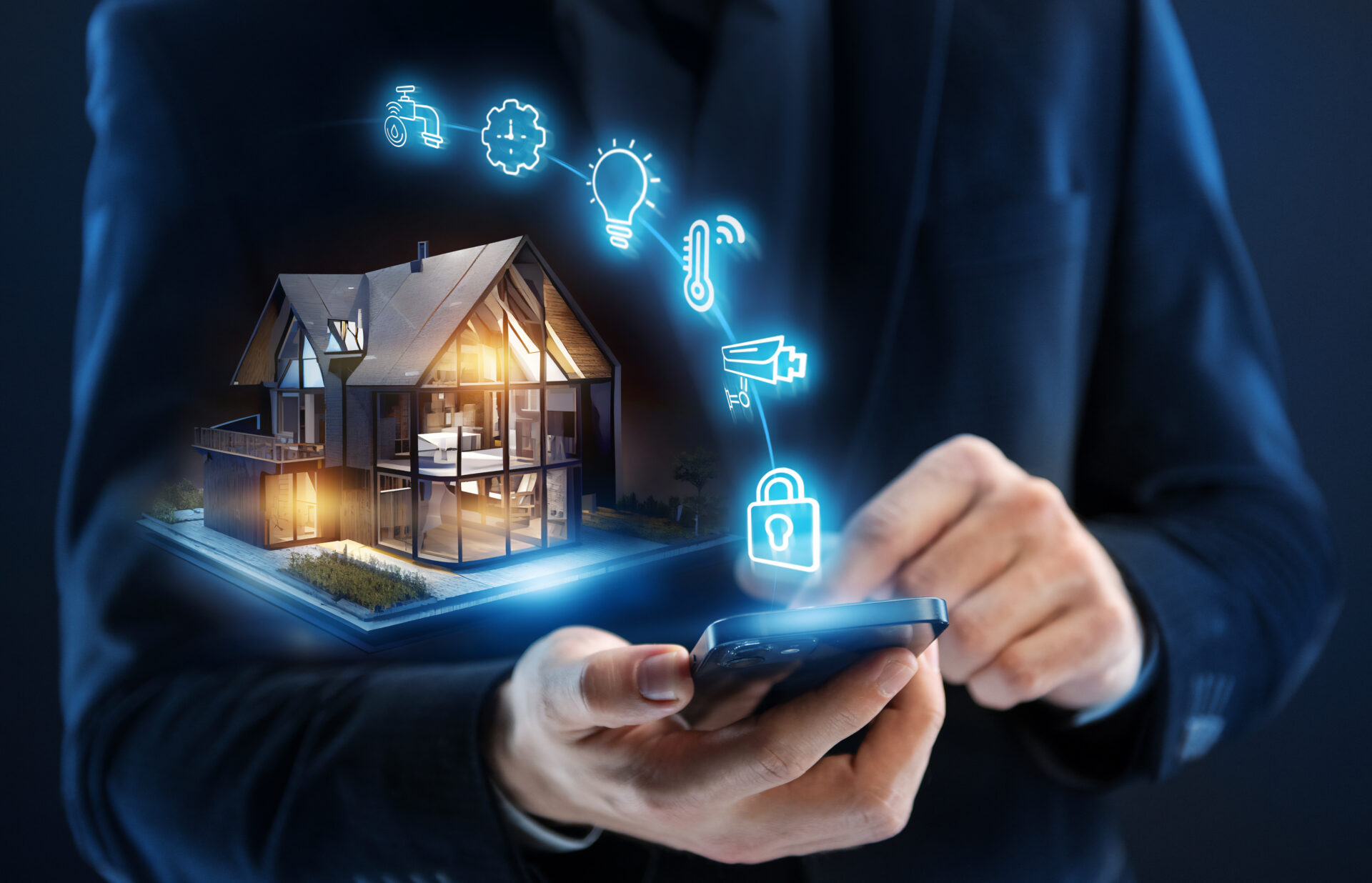
The system supports integration with multiple software, including MES system. Some brands’ hardware is compatible with Hermas criteria, supports localization service, and has independent R&D. The system also provides a complete database for tracking, analyzing trends, identifying bottlenecks, optimizing parameters, or making data-driven decisions. This data-centric approach fosters continuous improvement and innovation in PCBA manufacturing.
Post time: Mar-19-2025